Slot Partial Discharge
- Introduction – what causes partial discharge? Partial discharge (PD) occurs in high voltage (HV) electrical equipment like cables, transformers, motors and generators. It is a kind of very small spark that occurs due to a high electrical field. In industrial high voltage motors and generators, electrical stress can reach several kilovolts per.
- The varnish follows the wire into the entirety of the slot, eliminating chances for partial discharge in random windings. Once fully saturated, the current is increased in the windings, resulting in the varnish curing while on the machine.
The impact of humidity on the slot partial discharge (PD) process was evaluated in a laboratory experiment conducted in a climatic chamber under constant humidity and temperature. Two stator bars, subjected to slot PDs at two temperatures (28°C and 85°C), were aged at twice their nominal phase-to-ground voltage (16 kV) under three absolute.
Contribution of Electrical-Thermal Aging to Slot Partial Discharge Properties of HV Motor Windings
Abstract
During the operation of HV motor, the abrasion of stator windings because of vibration caused by electromagnetic force will lead to slot partial discharge (PD). Furthermore, the superheat induced by overcurrent or poor heat dissipation will aggravate the slot PD. To understand the developing process of slot PD and comprehend the influences of aging factors on slot PD properties, two discharge bar models were made under electrical-thermal aging. At triple the rated line-to-earth voltage of 6 kV, two stator bars were aged for 37 days under different temperatures. The slot PD was measured during different aging stages, and visual observations of the insulation and stator core surface were made at the beginning and the end of aging. The experiment results indicate that electrical-thermal aging has a significant impact on the slot PD activities. The slot PD was intense under higher thermal stress, and the surfaces of insulation and stator core were oxidized after the long-time aging. This study can provide a judging basis for fault diagnosis of HV motors.
- Electrical-thermal aging;
- Slot partial discharge properties;
- HV motor windings
After a motor is rewound, the windings must be further insulated with resin or varnish. This insulation protects the windings from contamination, shorting electrically, and also make the windings more mechanically rigid. There are four types of varnishing methods that we will describe below: Dip and Bake Epoxy Varnishing, Trickle Varnishing, Vacuum Pressure Impregnation, and Ultra-Sealed Winding.
Dip and Bake is a standard varnishing technique where the motor windings are dipped into a varnish tank and then set to cure in an oven. Typically, a new motor winding should be dipped twice (double dip and bake) to ensure the varnish fully covers the windings.
Many repair shops do not allow the windings to cool once they are cured in the oven after the first dip and before the motor is dipped a second time. Because the windings are still hot during the second dip, the varnish becomes more viscous and runs off the motor easily. This results in a less effective second dip of varnish.
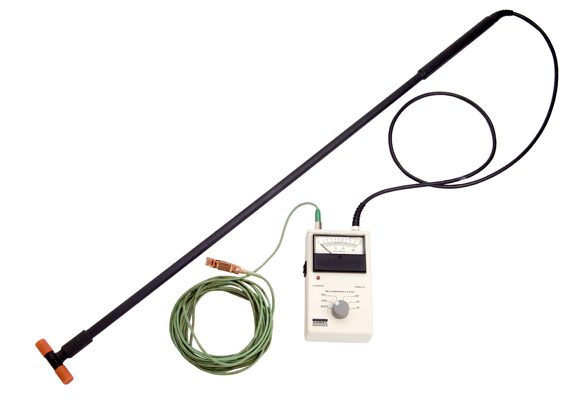
Because we want to ensure adequate varnish coverage, Dreisilker’s quality standards denote that the windings must be cool before the second dip. Our varnish is Class N and Hermetic rated, meaning the varnished used can withstand higher temperatures and is fit for compressors (respectively).
Trickle Varnishing The winding is connected to a rotating table and electrical wires. Using electrical resistance, the winding gets heated while spinning. Once at temperature, a tiny stream of varnish is trickled onto the winding head. The varnish follows the wire into the entirety of the slot, eliminating chances for partial discharge in random windings. Once fully saturated, the current is increased in the windings, resulting in the varnish curing while on the machine. This process is faster and better than the traditional dip and bake process because it cures on the machine – making it ideal for emergency repairs.
Slot Partial Discharge Procedure
Vacuum Pressure Impregnation (VPI) utilizes a vacuum pressure tank filled with varnish to fully impregnate motor windings and insulation with resin or varnish. At Dreisilker, we preheat our windings, place the windings in our 10 ft. diameter tank, draw a vacuum, fill the tank until the resin or varnish covers all of the winding, then pressurize the tank. These cycles are all set to various times and capacitance is monitored to determine the resin or varnish fill is acceptable. This process is typically used on medium voltage motors and form coil systems because traditional varnishing methods will not fully saturate the motor coils and their insulation tapes with varnish. The VPI method is the most time consuming process.
Slot Partial Discharge Symptoms
Ultra-Seal Winding is an alternative method of insulating a motor’s windings. Ultra-Sealed windings are completely impregnated and seals the coils with high molecular weight thermoset polymer resin. This allows for total protection against moisture, contaminants, and more efficient cooling. We recommend Ultra-Seal Windings for motors found in extreme environments, where contamination is likely. Want to learn more about Ultra-Seal Windings? Read our blog: How to Extend the Life of Your Servo and Spindle Motors in Extreme Environments